Process of electroplating
Electroplating is a process that involves the use of electrical current to deposit a thin layer of metal onto a surface. This process is used to improve the appearance, durability, and conductivity of a wide range of materials, including metals, plastics, and ceramics.
The electroplating process is a complex one that requires specialized equipment and skilled technicians. It involves immersing the object to be plated into a solution containing the metal ions, then passing an electrical current through the solution. This causes the metal ions to deposit onto the object, forming a thin and uniform layer.
Here is one example:
And this is how a large electroplating tank looks like on-site:
There are different types of electroplating, each one with its own specific uses and advantages. Some of the most common types of electroplating include:
- Copper plating: This process is used to improve the conductivity of a material, and it is also used as a base layer for other types of plating.
- Nickel plating: This process is used to improve the corrosion resistance and durability of a material.
- Chrome plating: This process is used to improve the appearance and durability of a material, it also increases the resistance to corrosion.
- Gold plating: This process is used to improve the appearance and conductivity of a material.
How are pumps used in the electroplating process?
Typical Applications of pumps
- Provide flow through eductors for mixing of plating tanks without introducing air.
- Provide flow through filters to keep plating solutions clean.
- Empty and refill tanks with plating solutions.
- Transfer chemicals and rinse waters from sumps.
- Transfer wastewater and water treatment chemicals in on-site treatment plants.
ARO in Electroplating 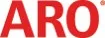
One of the main advantages of using ARO pumps in electroplating is their ability to handle highly corrosive fluids. The pumps are constructed with materials that are resistant to corrosion, such as stainless steel, aluminium, and thermoplastics. This allows them to withstand the harsh chemicals used in electroplating, such as acids and plating solutions.
Another benefit of ARO pumps is their ability to handle high-viscosity fluids. The diaphragm design of these pumps allows them to handle fluids with viscosities up to 15,000 cps, making them well-suited for use with thick plating solutions.
In addition to handling corrosive and high-viscosity fluids, ARO pumps are also able to handle high flow rates. These pumps can achieve flow rates up to 520 GPM, making them suitable for large-scale electroplating operations.
Finish Thompson in Electroplating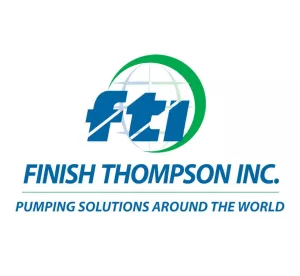
Plating shops that produce these finishes perform a wide range of filtration, mixing and cleaning, which require use of heavy-duty pumps in their systems to withstand the harsh materials involved. Finish Thompson is most renowned for their products corrosion resistance and reliability.
Other than its superior corrosion resistant materials, Finish Thompson’s Pumps have a a unique design that helps them handle fluids with viscosities up to 100,000 cps, making them well-suited for use with thick plating solutions.
Finish Thompson’s has a strong reputation of resolving Chrome Plating Challenges with its comprehensive pump product line. Check it out over here.
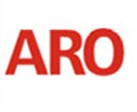
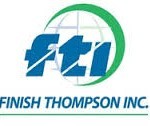